Cientistas criam plástico 100% reciclável: o mundo está preparado?
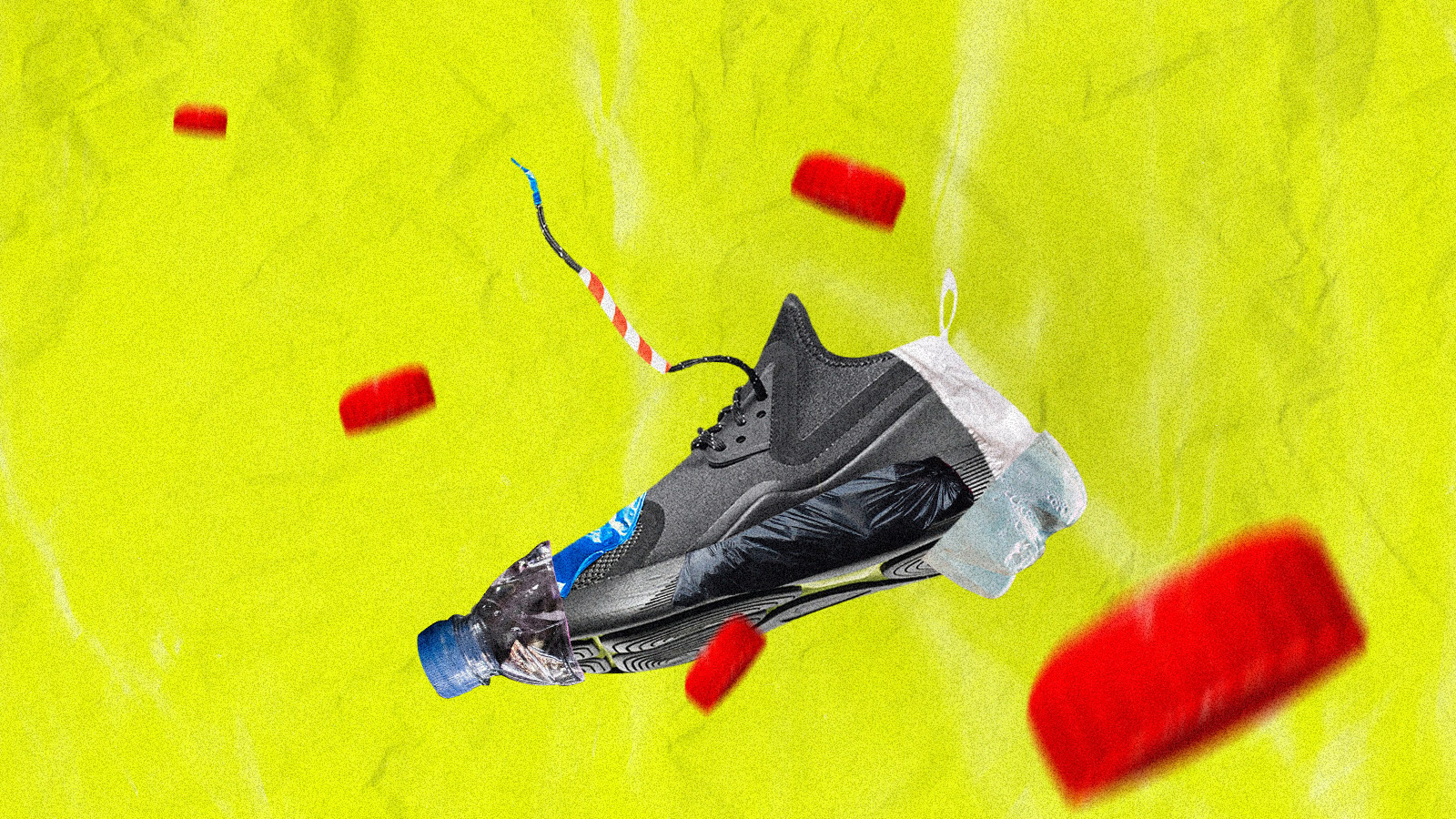
O estadunidense médio gera cerca de 100 quilos de lixo plástico a cada ano. A grande maioria não é reciclada, mesmo que você envie para uma usina de reciclagem. A maior parte do plástico acaba em um lixão.
Há diversas razões para isso acontecer. Algumas usinas de reciclagem não possuem tecnologia para separar o plástico corretamente. E, para as empresas, é realmente mais barato fazer plástico “virgem” do que produzir plástico reciclado. O plástico reciclado está longe de ser perfeito. Em geral, é produzido pelo derretimento de plástico velho, mas, na verdade, precisa de plástico virgem misturado para manter sua estrutura. Estima-se que 91% de todo o plástico não é reciclado.
Mas pesquisadores do Laboratório Nacional Lawrence Berkeley e do Departamento de Energia têm estudado um novo (e atrativo) tipo de plástico. Chamado de polidicetoenamina, ou PDK, o material é infinitamente reciclável. Pode ser 100% recuperado e remodelado em um novo item de plástico quantas vezes a empresa quiser.
Como um plástico novo pode ser melhor do que o velho? Nossos plásticos tradicionais, como galões de leite (feitos de polipropileno) e meias de náilon, foram desenvolvidos na década de 1930 para serem baratos e fáceis de produzir em massa a partir de subprodutos da indústria do petróleo. Sob este aspecto, eles foram milagrosos e possibilitaram avanços em bens de consumo, de garrafas compactas aos Tupperwares. O problema é que quase 100 anos depois, este material milagroso penetrou completamente em tudo o que usamos e fazemos – e está matando o planeta. Sendo realistas, não podemos eliminar o plástico da cadeia de abastecimento e, mesmo que o fizéssemos, isso não resolveria a crise climática mundial. Mesmo os materiais mais orgânicos, como algodão, drenam recursos naturais. É por isso que muitos especialistas estão defendendo que a reciclagem seja mais fácil – seja por meio dos próprios materiais, de usinas de reciclagem ou, de preferência, ambos.
“Estamos projetando novos polímeros pensando na facilidade de reciclá-los”, diz Corinne Scown, cientista da equipe e vice-diretora da seção do Laboratório Nacional.
Os plásticos são cadeias de moléculas idênticas chamadas monômeros, que se ligam aos polímeros como os conhecemos. Aditivos podem entrar na mistura, de corantes a retardantes de chama para personalizar o material para diferentes fins. Portanto, quando você tenta reciclar o plástico ao derretê-lo, todas as substâncias distintas se misturam até ficarem inseparáveis.
“[Hoje], derreter um plástico que tem todos os tipos de aditivos… tudo isso vai ficar lá”, explica Scown. “É claro que você terá um produto degradado no final desse processo.” E como o resultado é um material degradado, os fabricantes adicionam plástico virgem para tornar o produto mais resistente. Até mesmo os tênis Loop de última geração da Adidas, que permitem à empresa fundir um par antigo em um novo, exigem que plásticos virgens sejam adicionados à mistura. Na mesma linha, a Everlane, que está se esforçando muito para eliminar o plástico virgem, não encontrou substitutos adequados para itens como zíperes e elastano. A degradação do plástico reciclado é um grande motivo.
No entanto, plásticos PDK são fabricados de forma que possam ser derretidos, não por calor, mas por ácido. Este processo ácido é mais controlável. Ele separa claramente os monômeros dos aditivos. E todos esses monômeros podem ser reutilizados no próximo lote de plástico. A equipe de Scown realmente demonstrou, usando simulações avançadas, que essa abordagem poderia funcionar em escala. Sem calor, o processo é menos intensivo em carbono do que a reciclagem típica de plástico. E permite que mais plástico seja recuperado.
Afinal, o PDK poderia substituir todos os nossos outros plásticos? Do ponto de vista prático, provavelmente não. De acordo com Scown, produzir um lote virgem de PDK com os métodos atuais custa cerca de 10 a 20 vezes mais do que os plásticos normais, principalmente porque esse processo não foi aprimorado com eficiência ideal em escala. Além disso, a pegada de carbono inicial é pior devido a alguns produtos químicos especializados necessários para o processo. No entanto, com o tempo, à medida que um produto é reciclado continuamente, o PDK faz mais sentido. Uma métrica-chave que Scown descobriu é que é mais barato reciclar o PDK, mesmo que apenas uma vez, do que produzir um novo pedaço de plástico virgem típico.
“Ainda há muitos testes a serem feitos para entender para quais aplicações, embalagens e bens duráveis isso é bom e como podemos adaptar novos monômeros no futuro para obter as especificações que queremos”, afirma Scown. “Não é como se isso fosse substituir todos os plásticos de um dia para o outro. Haverá algumas aplicações em que funcionará e outras não.”
Em outras palavras, plásticos descartáveis – como sacolas plásticas – que atualmente acabam em nosso fluxo de resíduos podem não fazer sentido como PDKs. A produção dessas sacolas seria mais cara em uma indústria de margem estreita. E sem uma infraestrutura de coleta para reciclagem, o custo financeiro e ambiental da produção das sacolas PDK seria maior. “Talvez o material não produza embalagens de batata frita nem filme plástico”, diz Scown. “Em vez disso, você pode querer fazer um produto durável; talvez um que tenha um programa de devolução, ou um produto que seja mais um modelo de aluguel ou serviço em vez de compra.”
Na verdade, se você observar os produtos com mais etiquetas que uma empresa espera reciclar – como sapatos – e os PDKs de repente fazem muito sentido, já que o custo do material de plástico é uma parte muito pequena do preço geral do sapato. “Contanto que seja possível utilizá-lo em produtos que garantam a recuperação da grande maioria desse material para reciclar várias vezes, já será muito bom. Ao longo da vida útil do plástico, muitos ciclos de reciclagem, você está se aproximando de um custo semelhante ao dos plásticos que temos agora”, afirma.
A partir de agora, os pesquisadores estão procurando empresas privadas que possam querer fazer parceria para testar PDKs em uma escala mais ampla, enquanto continuam a desenvolver a tecnologia e ver como expandi-la para além do laboratório.